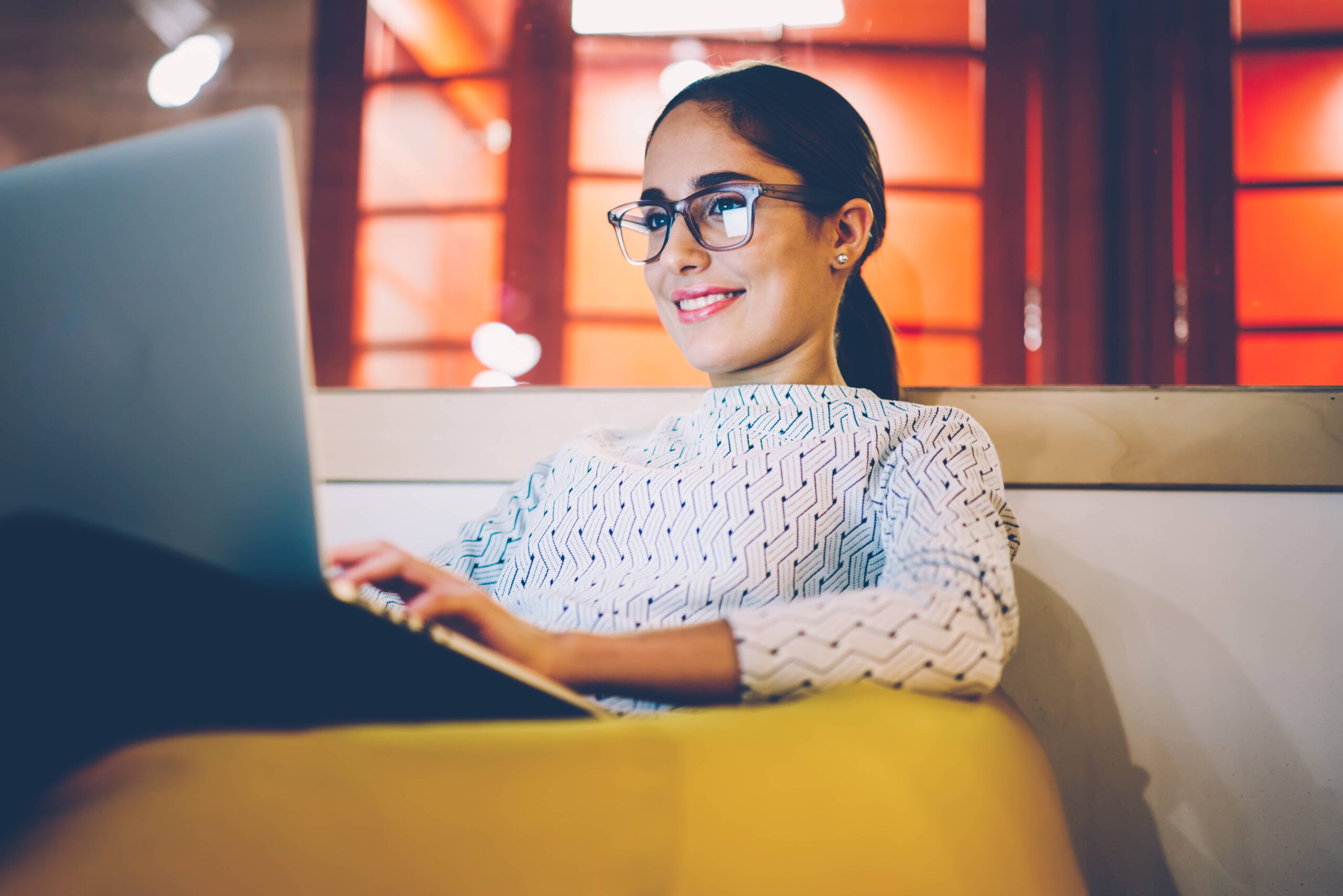
TO CONTRACT
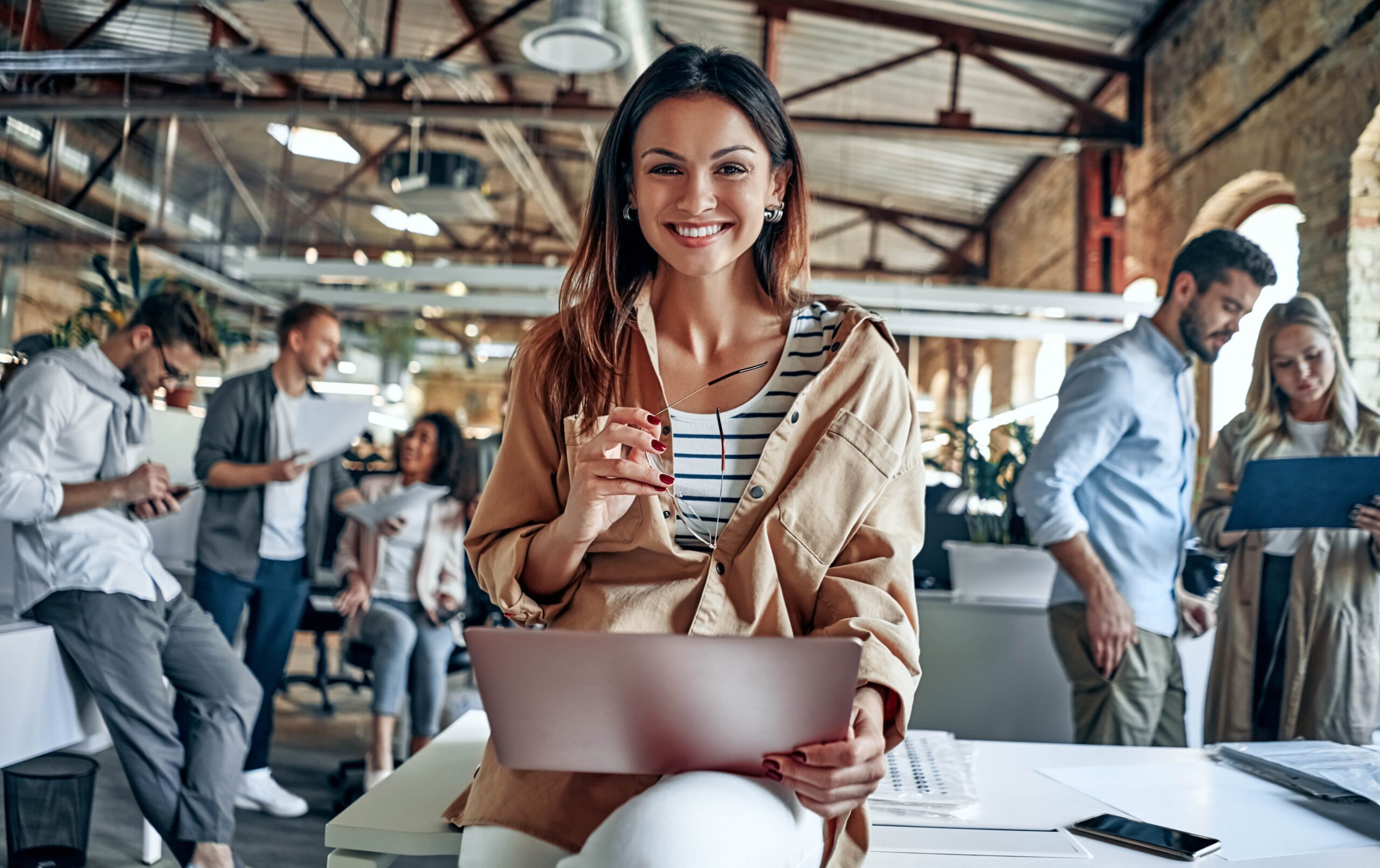
z dowolnego miejsca.
Monitoruj budżety, terminy i warunki handlowe swoich kontraktów.
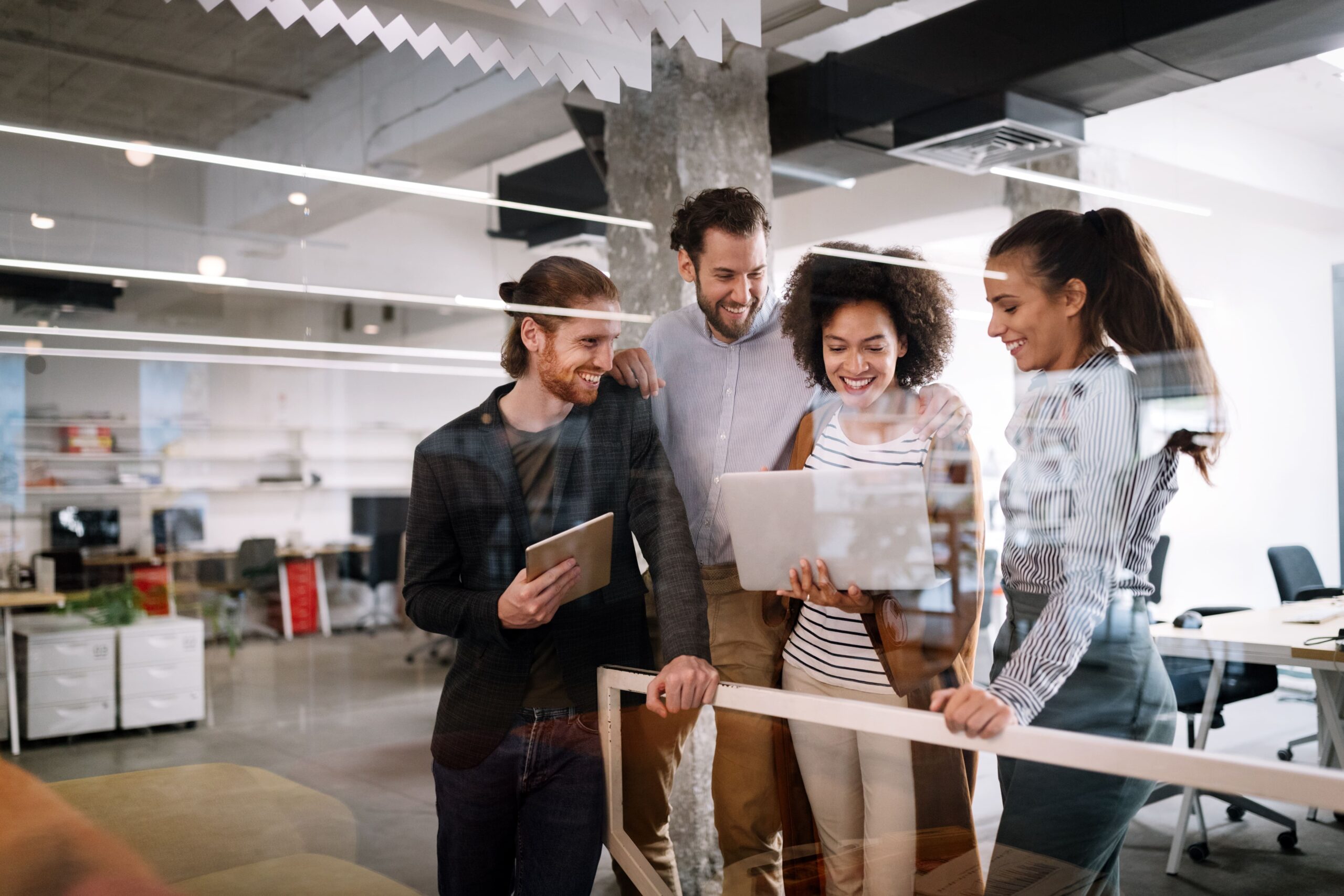
Otwórz przyjazny e-sklep dla pracowników i monitoruj wydatki.
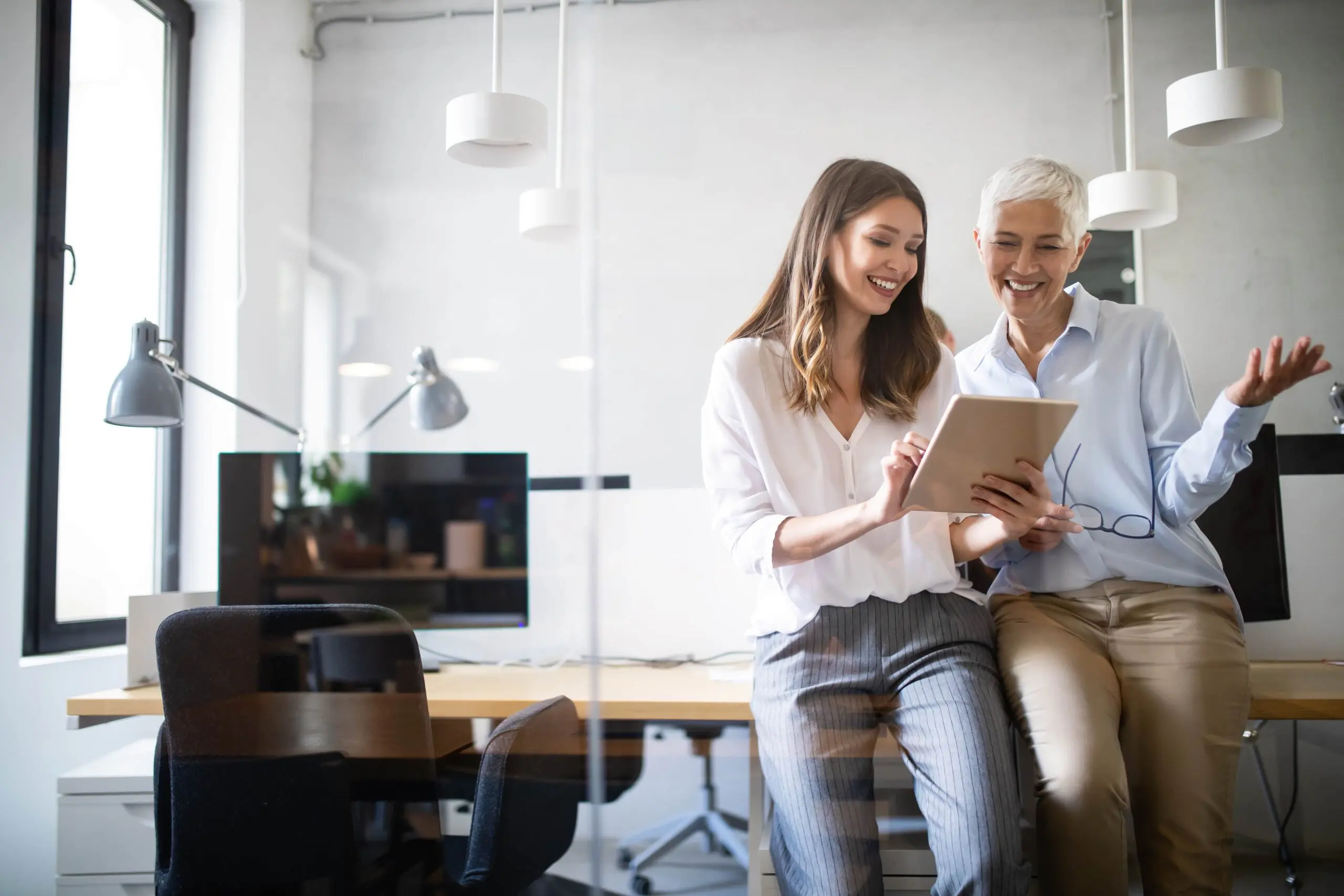
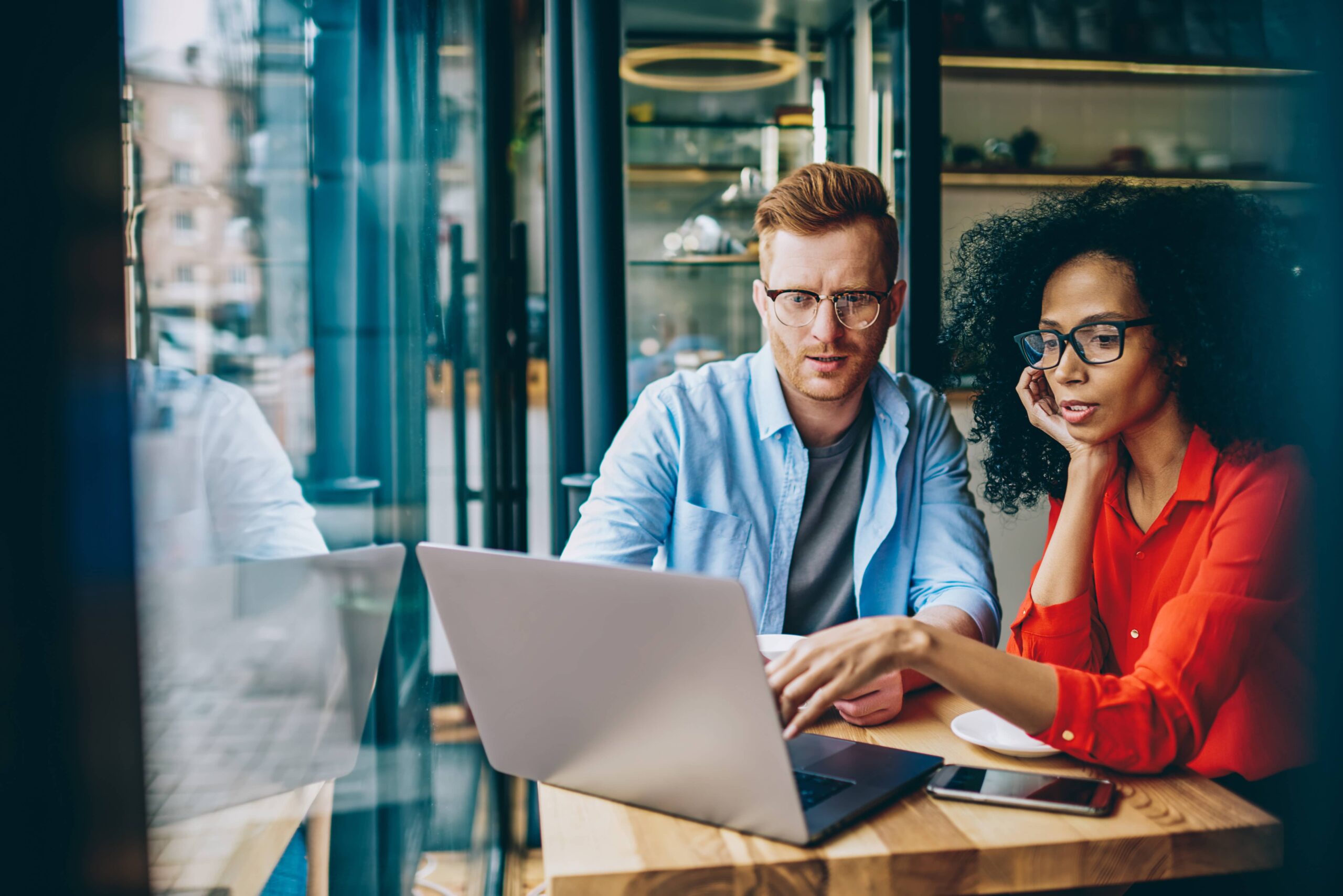
Marketplanet Cloud
Rozwijaj Twój B2B e-commerce – zakupy, płatności i rozliczenia skupione w jednym, przystępnym narzędziu w chmurze.
Marketplanet Cloud
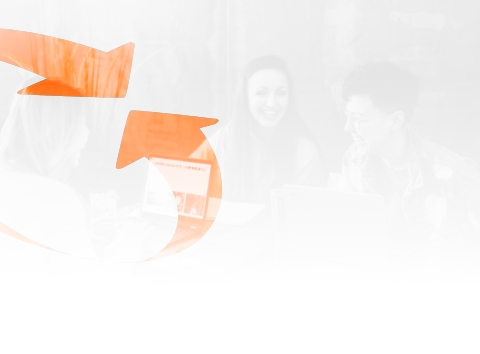
eZamawiający
Elektroniczna realizacja zamówień publicznych w jednym miejscu, intuicyjnie i zgodnie z ustawą Pzp.
eZamawiający
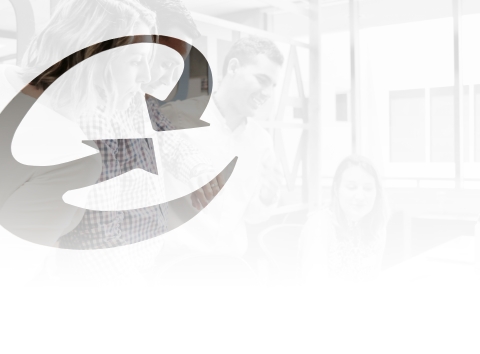
OnePlace
Współpracuj z obecnymi i nowymi dostawcami oraz kontrahentami.
OnePlace
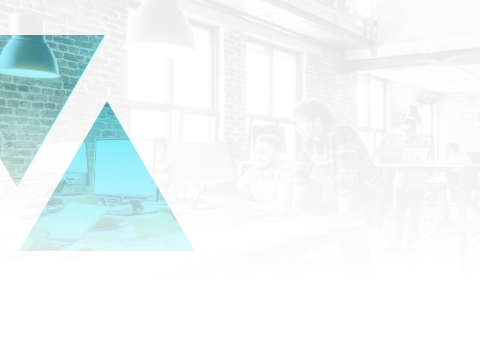
#ProcurementInfluencers
Twoje źródło wiedzy o finansach, zakupach i nowej technologii.
#ProcurementInfluencers
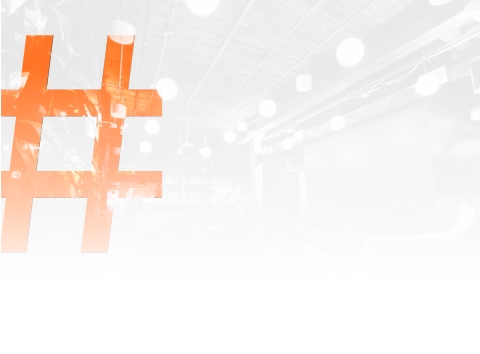
// Jesteśmy Marketplanet
W Markeplanet jesteśmy przekonani, że można łączyć pasję, biznes i cele ważne dla wszystkich, którzy z nami współpracują. To właśnie dlatego tworzymy oprogramowanie dla profesjonalistów. Marketplanet to miejsce spotkań ekspertów i partnerów, którzy chcą elektronizować świat B2B. Tworzymy rozwiązania e-commerce B2B, aby każdemu pracowało się łatwiej i prościej.
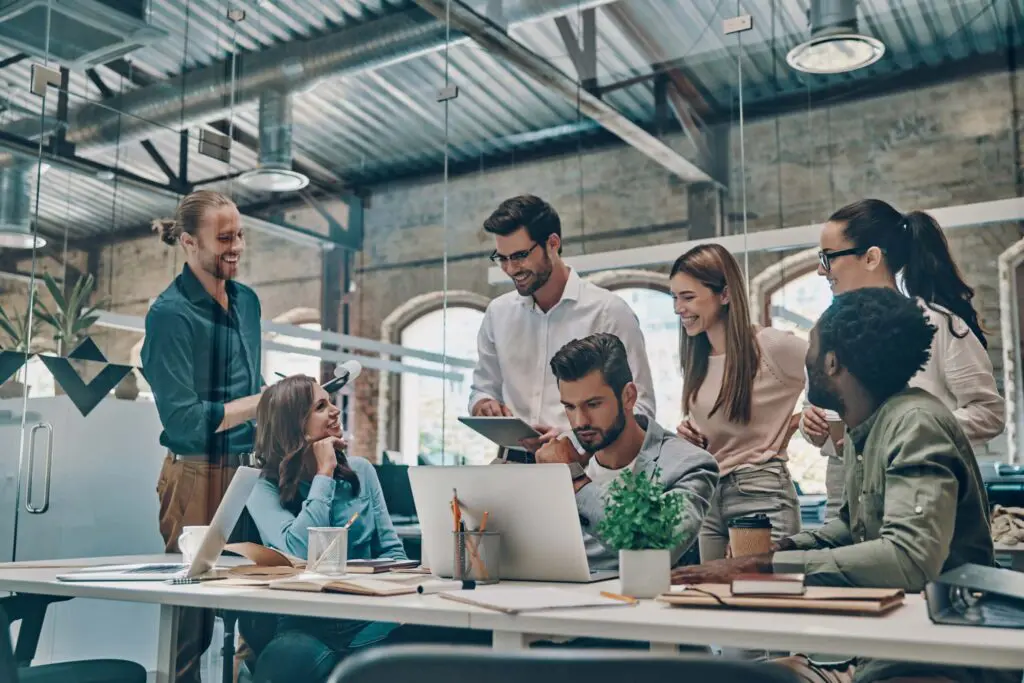
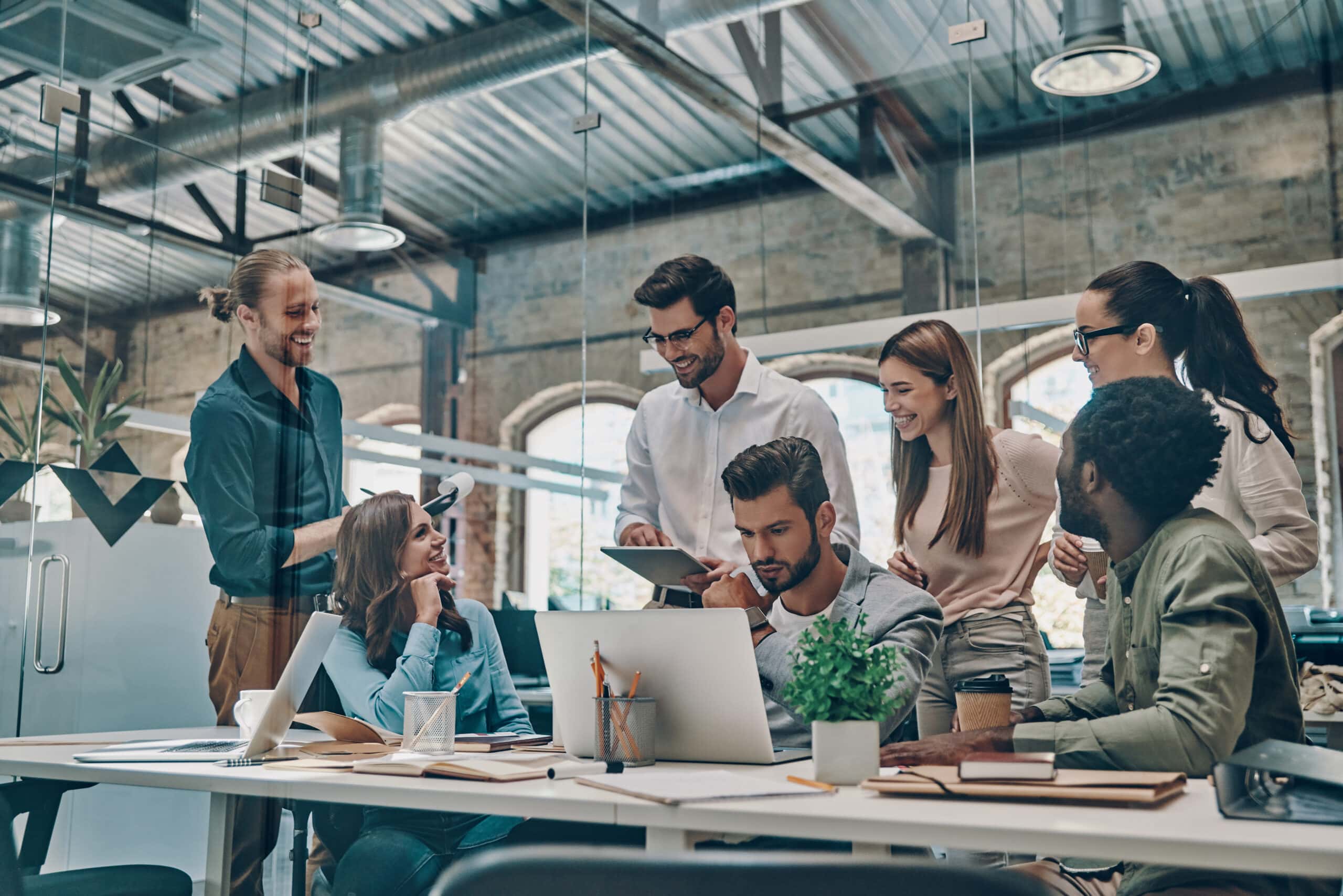
// Jesteśmy Marketplanet
W Markeplanet jesteśmy przekonani, że można łączyć pasję, biznes i cele ważne dla wszystkich, którzy z nami współpracują. To właśnie dlatego tworzymy oprogramowanie dla profesjonalistów. Marketplanet to miejsce spotkań ekspertów i partnerów, którzy chcą elektronizować świat B2B. Tworzymy rozwiązania e- commerce B2B, aby każdemu pracowało się łatwiej i prościej.
// Marketplanet
w liczbachTworzymy produkty, które ułatwiają życie wszystkim osobom w firmach.
w liczbach
Tworzymy produkty, które ułatwiają życie wszystkim osobom w firmach.
Czujemy się jak ryba w wodzie, wspierając kupujących i automatyzując rozliczenia zobowiązań. Dajemy poczucie pełnej kontroli poprzez łatwy dostęp do danych, co ułatwi Ci pracę, a Twoi współpracownicy pokochają nas za usprawnienie ich codziennej pracy
+
zadowolonych klientów
%
przedłużanych umów
tys.+
aktywnych firm na OnePlace
tys.+
dostawców w ekosystemie Marketplanet
+ mld
wartość zakupów naszych klientów
lat
doświadczenia
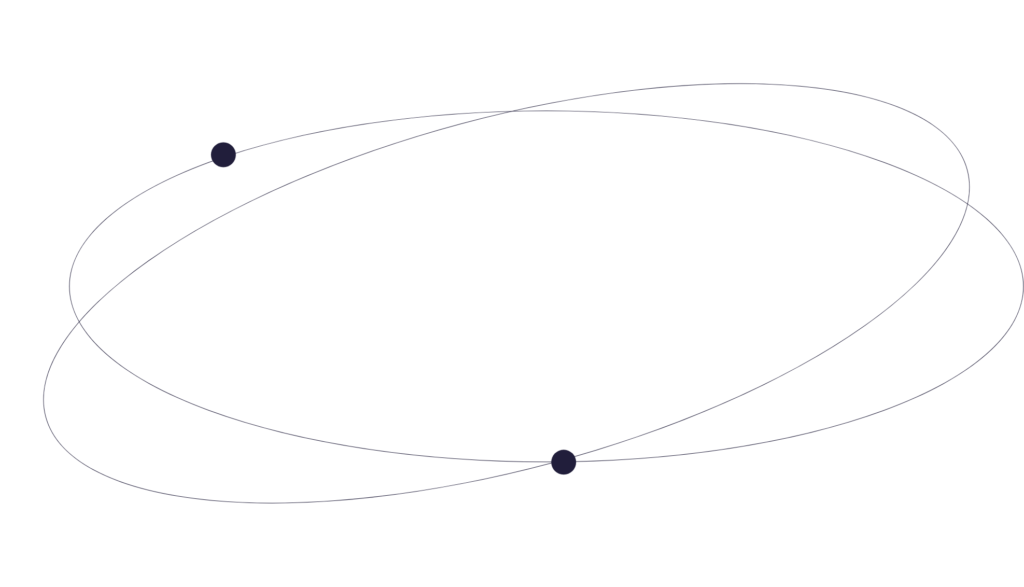
lat
doświadczenia
tys. +
aktywnych firm na OnePlace
tys. +
dostawców w ekosystemie Marketplanet
+ mld
wartość zakupów naszych klientów
%
przedłużanych umów
+
zadowolonych klientów
// Marketplanet
w liczbachTworzymy produkty, które ułatwiają życie wszystkim osobom w firmach.
w liczbach
Tworzymy produkty, które ułatwiają życie wszystkim osobom w firmach.
Czujemy się jak ryba w wodzie, wspierając kupujących i automatyzując rozliczenia zobowiązań. Dajemy poczucie pełnej kontroli poprzez łatwy dostęp do danych, co ułatwi Ci pracę, a Twoi współpracownicy pokochają nas za usprawnienie ich codziennej pracy.
// #PI
// ProcurementInfluencers
// Zaufali nam
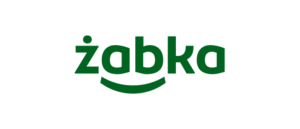
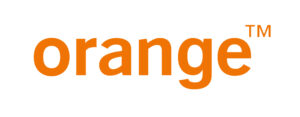
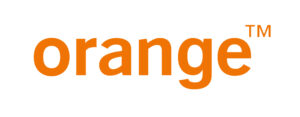
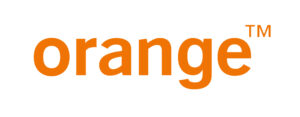
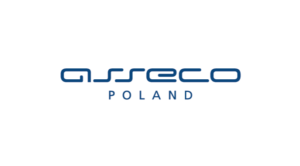
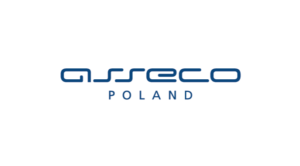
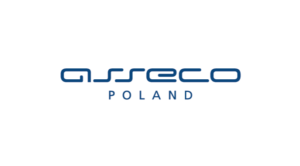
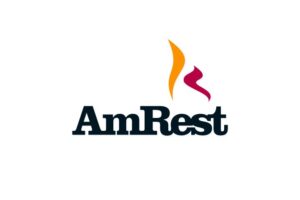
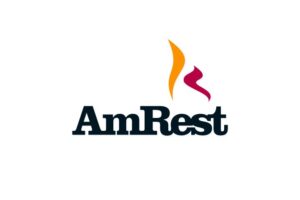
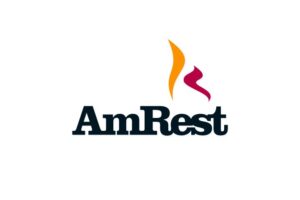
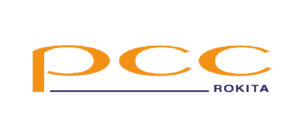
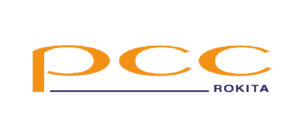
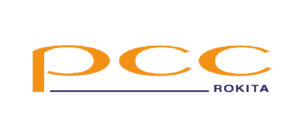
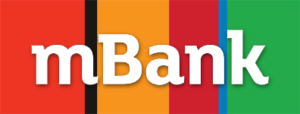
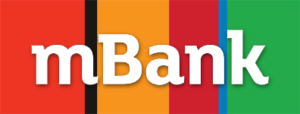
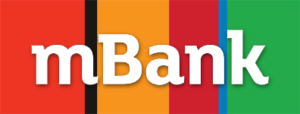
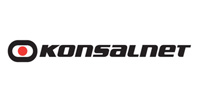
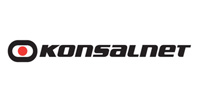
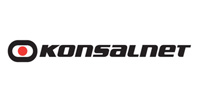
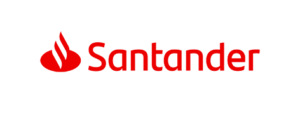
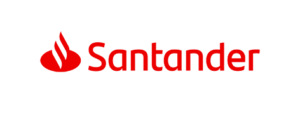
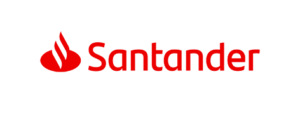
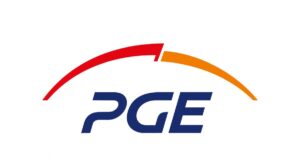
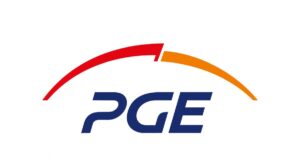
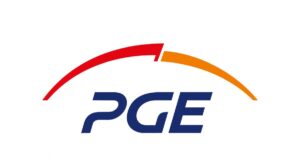
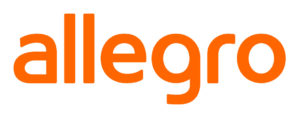
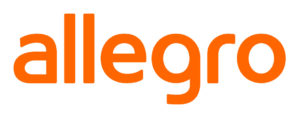
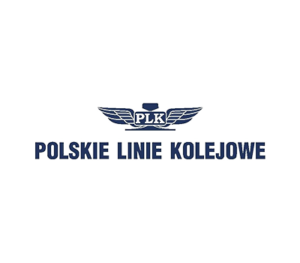
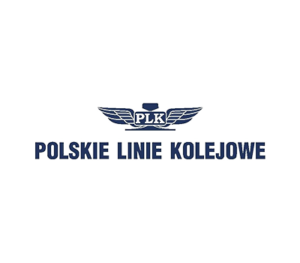
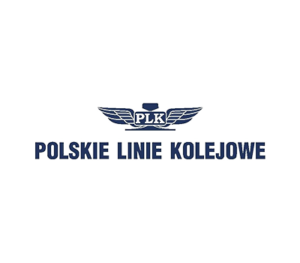
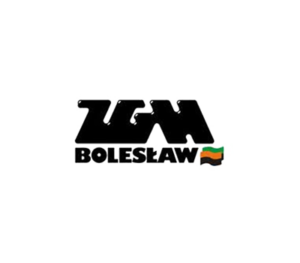
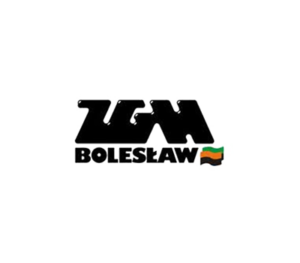
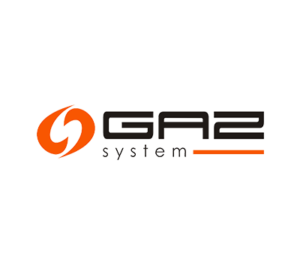
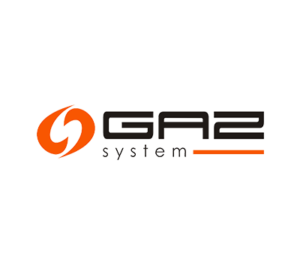
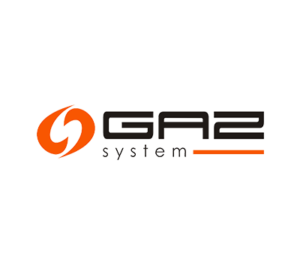
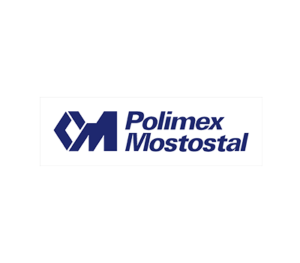
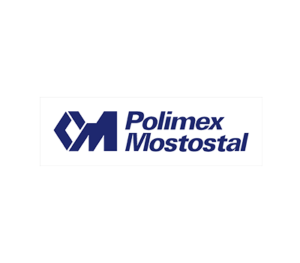
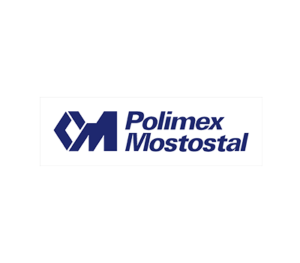
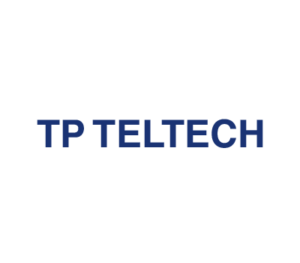
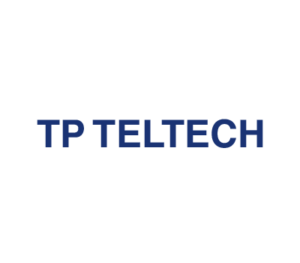
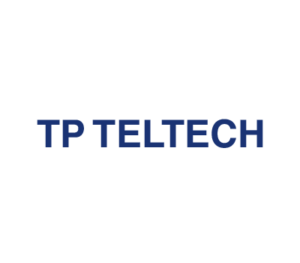
// Zaufali nam
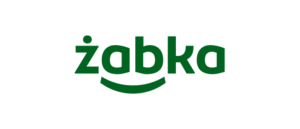
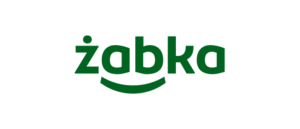
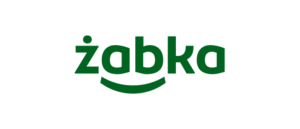
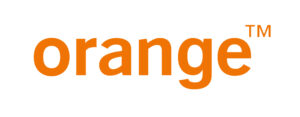
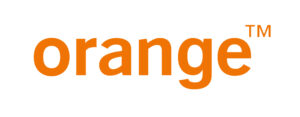
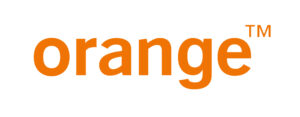
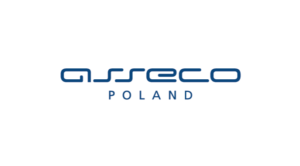
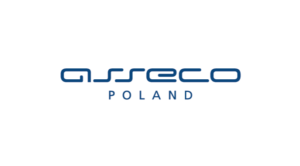
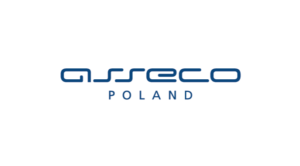
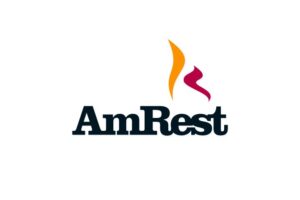
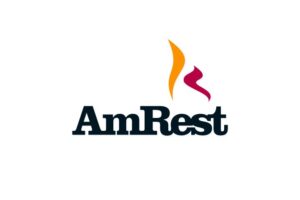
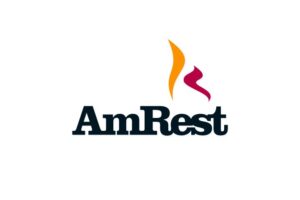
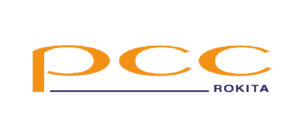
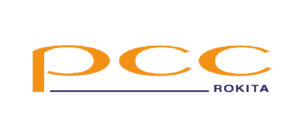
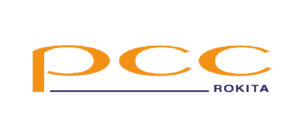
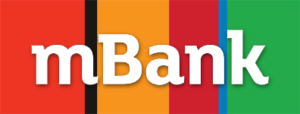
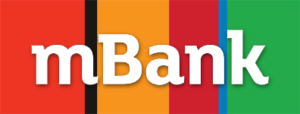
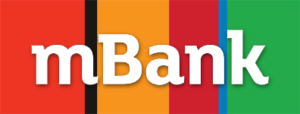
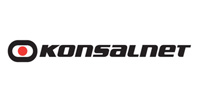
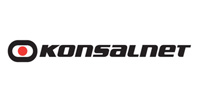
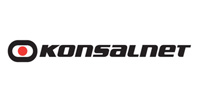
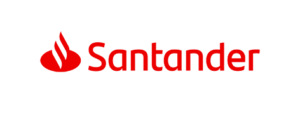
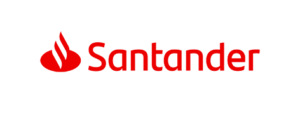
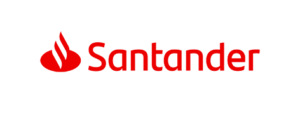
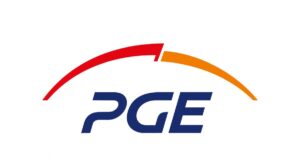
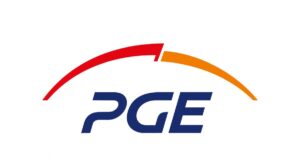
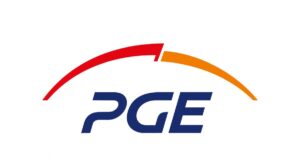
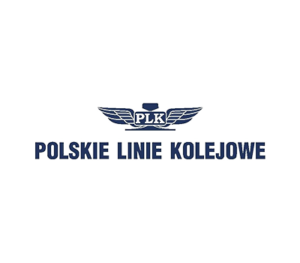
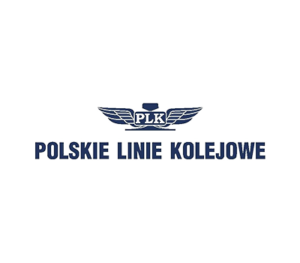
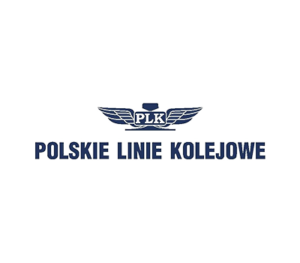
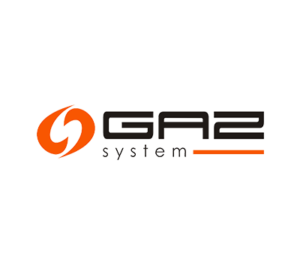
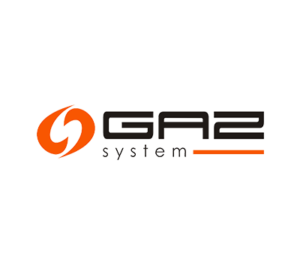
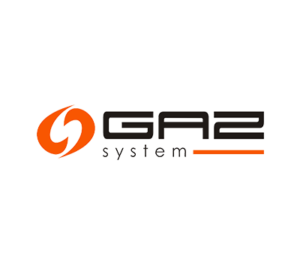
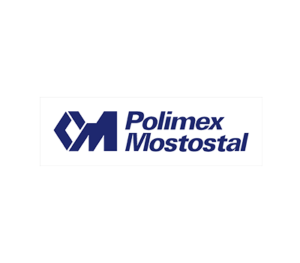
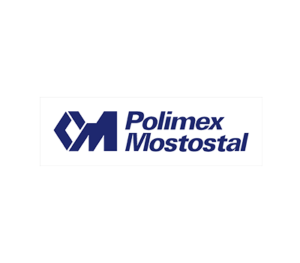
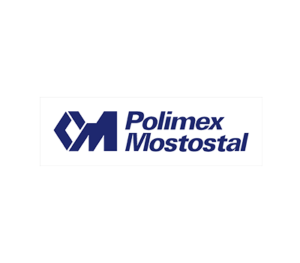
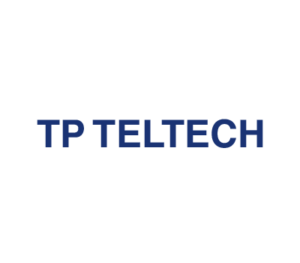
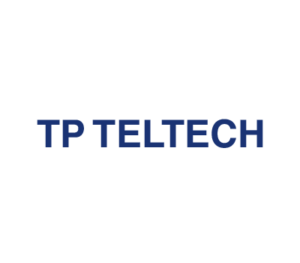
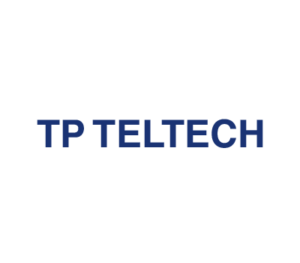
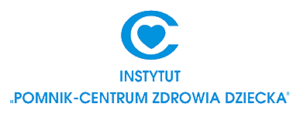
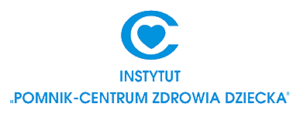
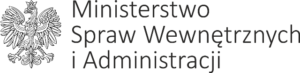
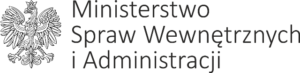
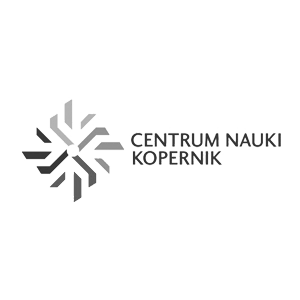
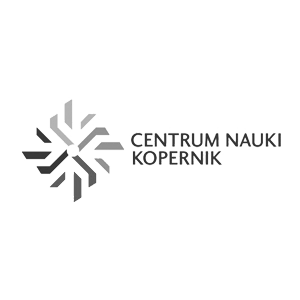
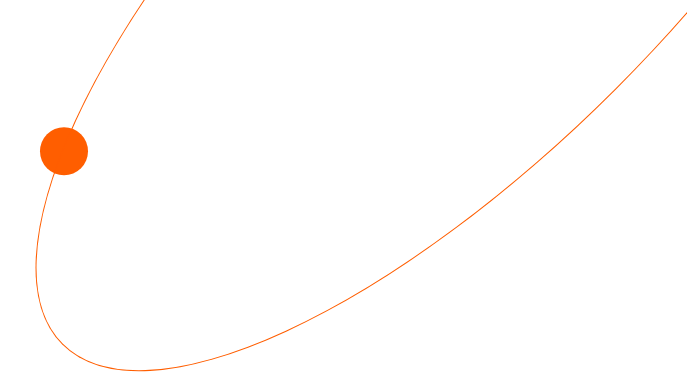
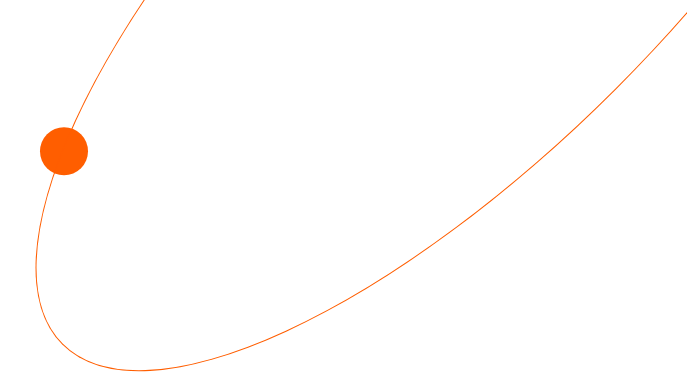